List Of Alloys And Their Composition And Uses Pdf To Jpg
What is the ratio of the composition of the two basic elements in alloy X? (A) 1: 1 (B) 2: 3 (C) 5: 2 (D) 4: 3 (E) 7: 9. Responding to a pm: When you need to find the average, it is better to use the formula in its original form: Avg = (C1*w1 + C2*w2)/(w1 + w2) Avg = [(5/8)*4 + (1/3)*3]/(4+3) = 1/2. Ratio of the 2. Alloys: Types, Properties, Composition and Uses of. Uses find below are some alloys and their uses. Types, Properties, Composition and Uses of.
Timber Cruise Excel Programs Classes there. Advanced Reinforced Concrete Design By Pc Varghese Pdf. This file type includes high resolution graphics and schematics when applicable. Gears are a common component of modern machinery, found in gearheads, watches, motors, furnaces, and automation equipment. Due to the ease of manufacturing and the variety of alloys available, metal alloys are the most common material used for gears. However, alternatives are available: ceramic and metal injection molding offer higher strengths and other properties that make them desirable. Metal Alloys and Gear Design The material used for gears depends on the strength and service conditions. Examples of service conditions are wear and noise.
Cast iron is a common gear material due to its good wearing properties, machinability, and the ease of producing complicated shapes via metal casting. Worm gears tend to use phosphor bronze because of the material’s wear resistance ability. Carbon or alloy steels are commonly used due to their high strength values. These steels are heat-treated in order to achieve the appropriate combination of toughness and tooth hardness. The hardness ranges of all three materials can be seen in the graph above. Bulk metallic glass sits in the middle of metals and ceramics as where metals are best for severe wear and ceramics are best for maximum hardness. And hardness is an important factor in gear design: The higher the hardness of the material, the more that the size and the weight of the gear used can be reduced.
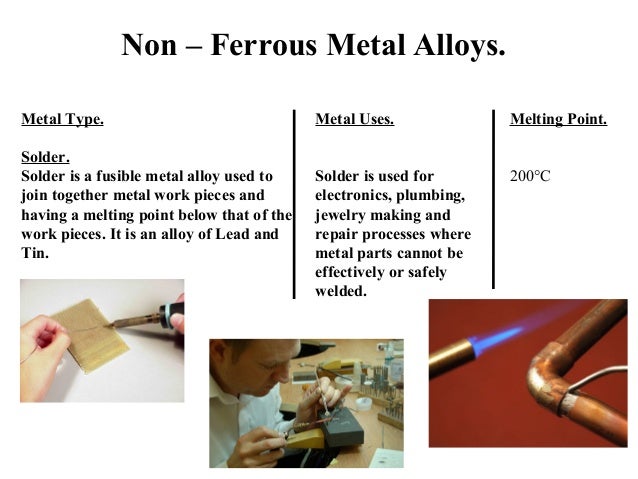

For example, let us compare two gear sets where the first set has a Brinell Hardness Number (BHN) of 2,000 N/mm 2 and the second set has a BHN of 6,000 N/mm 2. Due to higher hardness found in the second set, the gear set is smaller and has a more compact design. The weight of the second set is only 1/8 of the first set while still delivering the same power. Higher hardness also indicates surface durability or wear strength. The higher surface durability, the greater ability it has to resist tooth surface failure, or “pitting”—e.g., a fatigue caused by contact stress.
Surface durability is a function of compressive strength with directionally proportional to hardness. Surface hardening is commonly achieved by case-hardening processes: producing a hard case on the gear surface, but leaving the core soft. This is done, opposed to through hardening, because increased hardness can result in more brittle material. Some examples of hardness values are for cast iron grade 35 has a BHN of 300 N/mm 2 minimum. Phosphor bronze centrifugal cast has a BHN of 90 N/mm 2. AISI 9310 is a case-hardened steel alloy at 300°F used for aerospace gears that experience high loads and operate at high pitch line velocities.
The BHN value for AISI 9310 is 250 to 350 N/mm 2. Ceramic and Metal Injection Gears When choosing an alternative material for gears, ceramic and metal injected materials have become popular choices. The simple reason why is that for small-size applications that need to be highly wear-resistant, ceramics and metal injection pieces can be manufactured in large batches and are easier to produce than typical steel alloys.
The gearhead above from Maxon Motors uses a ceramic axis which has a max continuous torque of 0.5 to 2.0 Nm and longer lifetime against wear when compared to metal alloys. Both materials are created via the injection molding process. Ceramic and metal powders are prepared as feedstock. Zirconia Oxide (ZrO 2) is a common ceramic used for the injection process. For metal powders, the user can prepare their desired alloy composition blend. An example blend is the 316L composition of iron, copper, nickel, and molybdenum (FeCr 19Ni 9Mo 2), which is used for its combined strength and corrosion resistance. Aluminum oxide (AlO 2) is another common metal powder.
Wax and polymer binding additives are heated with ceramic and metal powder. Once cooled, they are processed into granular pellets for the feedstock. The powder is then processed on injection molding machines. The injection molded parts are called green compacts. Once out of the machine, the green compacts are then debindered. Debindering extracts the binding material from the green compact.